Benefits of Using High-Quality Hydraulic Oil Seals in Heavy Machinery
Ensure leak-free performance with high-quality hydraulic oil seal designed for durability, pressure resistance, and optimal sealing in tough conditions.
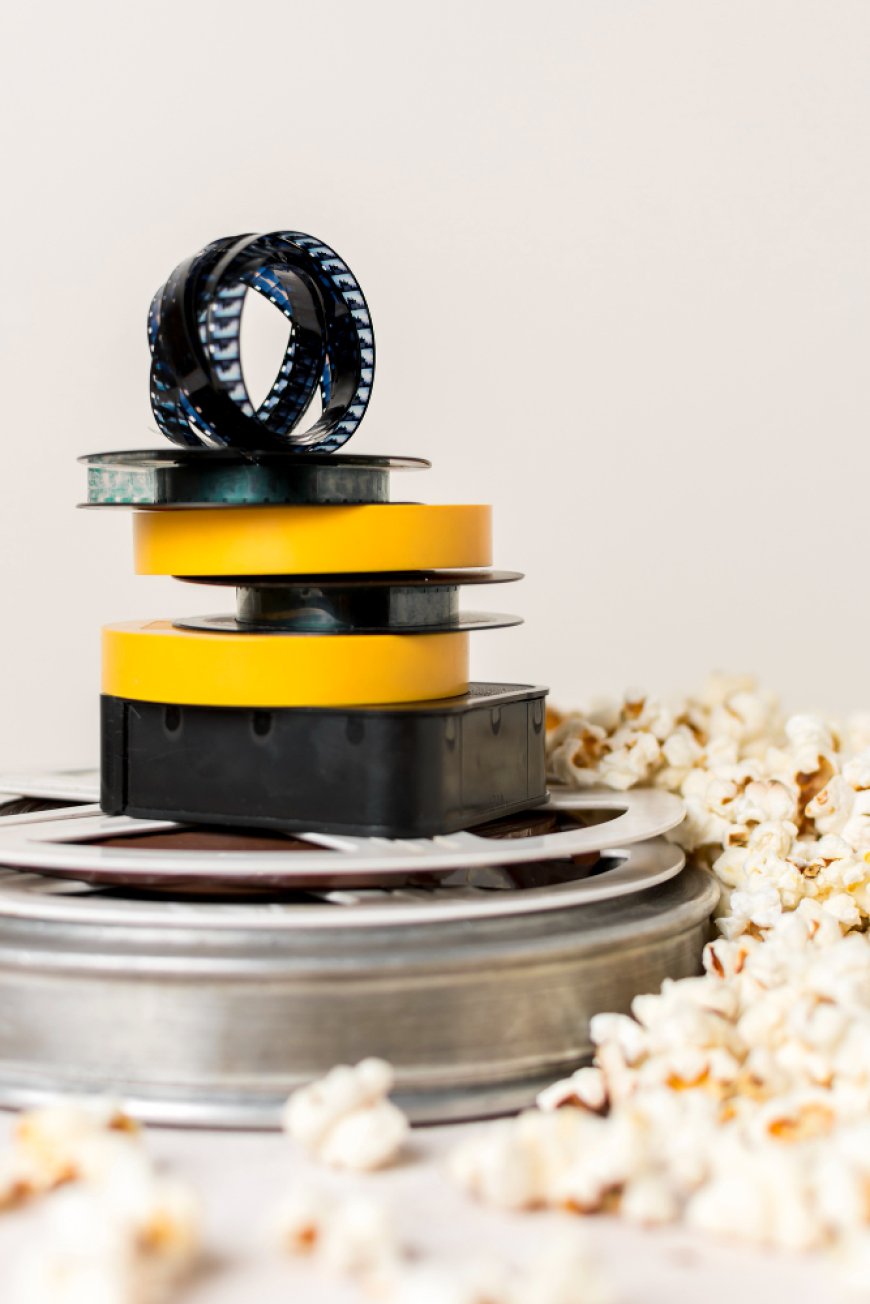
Introduction
In the world of industrial engineering and heavy machinery, precision and performance are non-negotiable. Equipment such as hydraulic presses, excavators, loaders, and lift systems operate under intense pressure and demanding conditions. One of the most critical yet often overlooked components ensuring optimal functionality is the hydraulic oil seal. These small but powerful devices play a pivotal role in preventing fluid leakage, maintaining pressure, and protecting internal components from contaminants.
Understanding the benefits of high-quality hydraulic oil seals not only ensures longer machinery lifespan but also significantly reduces operational costs and downtime.
Why Hydraulic Oil Seals Matter
Hydraulic systems depend on fluid power to function. This involves moving oil or fluid under high pressure through a network of pistons, cylinders, and valves. If this fluid escapes the system due to improper sealing, it can result in decreased efficiency, overheating, and even system failure. Hydraulic oil seals are designed to retain the fluid within the system while preventing dirt, dust, and moisture from entering. The right seal can make the difference between seamless operation and costly repairs.
Key Benefits of Using High-Quality Hydraulic Oil Seals
1. Enhanced Equipment Efficiency
High-quality seals maintain a strong barrier that prevents internal fluid from leaking. This retention of hydraulic fluid ensures that the machine operates with consistent pressure, translating into improved power output and responsiveness. Efficient fluid containment leads to better energy transfer and overall system performance.
2. Prolonged Machinery Lifespan
Contaminants such as dust, water, and metal particles can cause severe damage to internal components. A well-manufactured hydraulic oil seal acts as a gatekeeper, ensuring these harmful elements do not enter the hydraulic system. As a result, internal parts such as pistons and cylinders are protected, leading to reduced wear and longer operational life.
3. Reduced Maintenance and Downtime
Frequent maintenance is a significant burden on productivity, especially in industries where every second of downtime impacts revenue. Reliable hydraulic oil seals minimize the chances of system failures and leakage, leading to fewer maintenance intervals. This reduction in service requirements also brings down labor costs and increases machine availability.
4. Better Safety and Reliability
Faulty seals can result in hazardous leaks, particularly in environments with hot fluids or chemicals. Using seals that meet high-quality standards ensures that the hydraulic system remains sealed even under extreme temperatures and pressures. This enhances workplace safety and reduces the risk of equipment malfunction.
5. Cost Efficiency Over Time
While premium seals may carry a higher upfront cost, their durability translates to substantial long-term savings. Lower failure rates, reduced oil consumption, and minimal system damage contribute to a more cost-effective operation. Businesses can allocate resources more efficiently without worrying about unexpected equipment issues.
Applications That Demand High-Quality Sealing Solutions
Heavy-duty industries rely on hydraulic systems for a broad range of functions, from lifting and pushing to braking and steering. Applications where premium hydraulic oil seals prove indispensable include:
-
Construction Equipment: Excavators, bulldozers, and loaders operate in dust-heavy and high-impact environments, making robust sealing crucial.
-
Agricultural Machinery: Tractors and harvesters encounter muddy, wet, and varied terrains, requiring reliable seals to withstand diverse conditions.
-
Manufacturing Systems: Hydraulic presses and injection molding machines operate continuously under high pressure, necessitating effective sealing for optimal performance.
-
Aerospace and Defense: Precision, reliability, and environmental resistance are critical in aerospace applications, where seal failure is not an option.
These industries demand hydraulic seals capable of enduring challenging environments while ensuring uninterrupted performance.
The Role of Material and Design in Seal Performance
Not all seals are created equal. The material and design of a hydraulic oil seal can significantly impact its effectiveness. Depending on the application, materials such as polyurethane, nitrile rubber, PTFE, or Viton may be used. Each offers varying degrees of resistance to pressure, temperature, and chemical exposure.
Additionally, seal design—including lip shape, pressure relief features, and spring-loaded components—contributes to how well the seal manages fluid retention and contaminant exclusion. Engineers must evaluate these parameters to select the most suitable seal for their machinery.
Broader Industrial Benefits of Reliable Hydraulic Systems
Hydraulic systems are often paired with other pressure-based components like hydraulic road blockers in industrial and security applications. These devices rely on precise sealing and pressure control to function correctly. For example, in safety and access control environments, the advantages and applicable locations of hydraulic road blockers demonstrate how essential hydraulic systems are to both functionality and reliability.
Whether applied to security barriers or industrial lifting equipment, maintaining high seal integrity ensures smooth operation, enhances safety, and extends equipment life across a variety of sectors.
Conclusion
Investing in high-quality hydraulic oil seals is more than just a maintenance decision—it’s a strategic move toward maximizing machinery efficiency, safety, and longevity. These seals form the foundation of a reliable hydraulic system, preventing fluid leaks, protecting internal components, and enabling smooth performance under harsh conditions.
As industries continue to push the boundaries of what heavy machinery can achieve, the importance of durable, precise sealing solutions will only grow. By prioritizing quality and proper selection, businesses can safeguard their operations, minimize costs, and extend the life of their most critical equipment.