Screw Air Compressor: Reliable Power for Continuous Operation
This type of compressor is designed for continuous operation and delivers a consistent flow of compressed air—making it ideal for heavy-duty industrial applications.
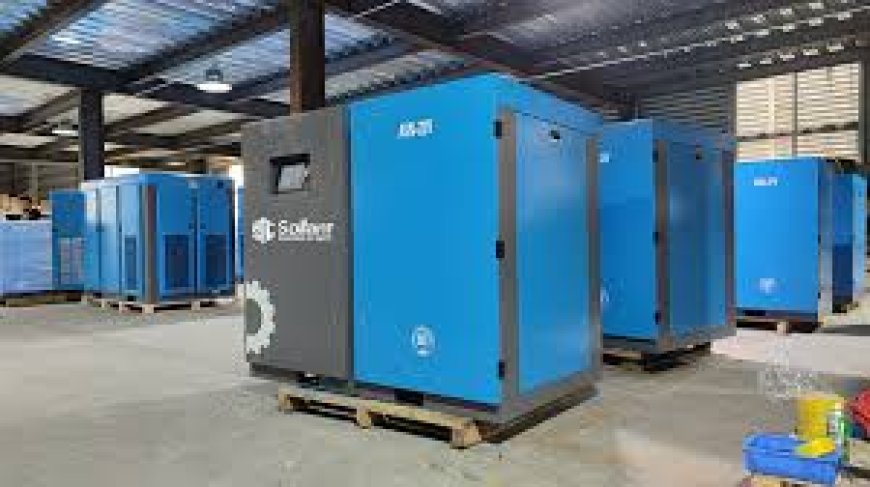
In modern industries, where efficiency and reliability are non-negotiable, the screw air compressor stands out as one of the most trusted types of compressed air systems. It provides a steady supply of compressed air, is highly efficient for continuous use, and is a top choice in sectors like manufacturing, automotive, food processing, and pharmaceuticals.
What is a Screw Air Compressor?
A screw air compressor (also known as a rotary screw compressor) is a type of positive displacement compressor that uses two helical screws (rotors) to compress air. These rotors rotate in opposite directions, trapping air between them and reducing its volume as it moves along the screws, which increases the air pressure.
This type of compressor is designed for continuous operation and delivers a consistent flow of compressed air—making it ideal for heavy-duty industrial applications.
How Does a Screw Air Compressor Work?
The operation of a screw air compressor involves four key stages:
-
Air Intake: Ambient air is drawn into the compression chamber through an inlet valve.
-
Compression: Two interlocking helical rotors compress the air as it moves through the chamber.
-
Cooling and Lubrication: In oil-injected models, oil is used to cool, seal, and lubricate the moving parts.
-
Air Discharge: The compressed air is separated from oil (if used), filtered, and then sent to the air receiver or directly to the point of use.
This simple, yet effective mechanism allows screw air compressors to operate with low vibration, minimal maintenance, and high energy efficiency.
Types of Screw Air Compressors
There are two main types:
-
Oil-Injected Screw Compressors: Use oil for cooling and lubrication; suitable for general industrial use where some oil content is acceptable in the air output.
-
Oil-Free Screw Compressors: Designed for applications requiring 100% clean air, such as in pharmaceuticals, electronics, and food industries.
Advantages of Screw Air Compressors
✅ Continuous Operation – Can run 24/7 with minimal downtime.
✅ Energy Efficiency – Especially when equipped with variable speed drives (VSD).
✅ Low Maintenance – Fewer moving parts reduce wear and tear.
✅ Quiet Performance – Quieter than piston compressors, making them suitable for indoor use.
✅ Compact Design – High power-to-size ratio allows for space-saving installations.
Common Applications
Screw air compressors are found in a wide range of industries, including:
-
Manufacturing Plants
-
Automotive Workshops
-
Food & Beverage Processing
-
Pharmaceutical Production
-
Textile and Chemical Industries
-
Mining and Construction Sites
Any industry that requires a constant flow of compressed air for tools, machines, or processes can benefit from the screw compressor’s reliable performance.
Choosing the Right Screw Air Compressor
To select the right model for your needs, consider the following:
-
Air flow (CFM or m³/min)
-
Operating pressure (PSI or bar)
-
Duty cycle requirements
-
Oil-lubricated vs. oil-free
-
Energy efficiency (look for VSD features)
-
Noise level and installation space
Consulting with a supplier or compressor expert can help ensure your investment delivers long-term performance and energy savings.
Conclusion: Why Choose a Screw Air Compressor?
If your operations demand consistent, reliable compressed air with minimal downtime, a screw air compressor is an excellent solution. Its robust design, energy efficiency, and low maintenance requirements make it the preferred choice in industries where productivity and performance are paramount.
Invest in a high-quality screw compressor today and experience the benefits of advanced air compression technology that keeps your business running smoothly.