Air Compressor: The Essential Powerhouse Behind Modern Industry
Compressed air is often referred to as the “fourth utility,” following electricity, gas, and water—underscoring its importance in industrial operations.
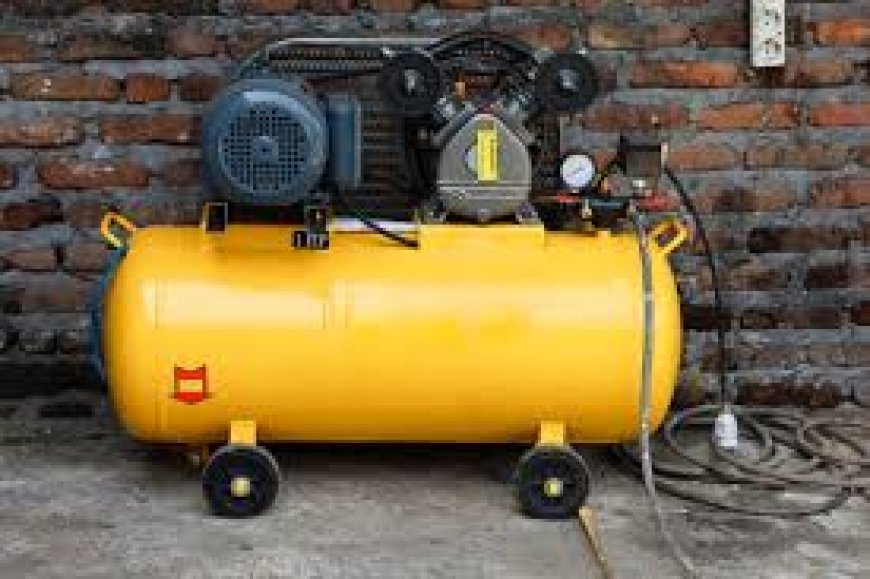
An air compressor is one of the most versatile and widely used machines in both industrial and home settings. From inflating tires to powering heavy-duty tools in manufacturing plants, air compressors provide a reliable source of compressed air that drives productivity, efficiency, and innovation across countless applications.
What is an Air Compressor?
An air compressor is a mechanical device that converts power (from an electric motor, diesel engine, or gasoline engine) into potential energy stored in pressurized air. This compressed air can then be released in controlled bursts to power tools, machinery, and various systems.
Compressed air is often referred to as the “fourth utility,” following electricity, gas, and water—underscoring its importance in industrial operations.
Types of Air Compressors
Air compressors come in several types, each designed for specific uses:
1. Reciprocating (Piston) Compressors
-
Ideal for low- to medium-demand applications.
-
Use pistons to compress air into a tank.
-
Common in automotive repair, construction, and home garages.
2. Rotary Screw Compressors
-
Designed for continuous operation in industrial settings.
-
Use two rotating screws to compress air.
-
Energy-efficient and durable; ideal for factories and large workshops.
3. Centrifugal Compressors
-
Used for high-volume air needs.
-
Operate at high speeds and are commonly found in large-scale facilities like chemical plants and refineries.
How Does an Air Compressor Work?
The basic operation involves:
-
Intake of air into a compression chamber.
-
Compression of the air by mechanical means (pistons, screws, or impellers).
-
Storage of the compressed air in a tank (for some types).
-
Release and regulation of air for various applications.
Some air compressors are oil-lubricated, while others are oil-free, depending on the need for air purity and application sensitivity.
Key Applications of Air Compressors
Air compressors play a vital role in industries such as:
-
Manufacturing & Assembly Lines
-
Automotive and Tire Services
-
Construction Sites
-
Pharmaceutical and Food Production
-
HVAC and Refrigeration
-
Medical and Dental Equipment
They’re used for tasks like powering pneumatic tools, spray painting, sandblasting, material handling, and controlling automation systems.
Benefits of Using Air Compressors
✅ Versatile Power Source – Powers a wide range of tools and systems.
✅ Efficient and Reliable – Designed for long-lasting, consistent output.
✅ Cost-Effective – Reduces the need for multiple power sources.
✅ Safe for Use – Especially in environments where electrical sparks could be hazardous.
✅ Portable Options Available – Great for on-the-go applications.
Choosing the Right Air Compressor
When selecting an air compressor, consider:
-
Air flow requirements (CFM)
-
Operating pressure (PSI)
-
Duty cycle (continuous vs. intermittent)
-
Power source (electric, gas, diesel)
-
Tank size and portability
-
Noise levels
-
Oil-free vs. oil-lubricated design
Matching your compressor to your application ensures maximum efficiency and lifespan.
Conclusion: The Power Behind Productivity
Whether you’re operating a massive industrial facility or running a small home workshop, an air compressor is an invaluable tool. It delivers clean, consistent, and efficient power for a multitude of applications. By understanding your needs and selecting the right type and size, you can ensure optimal performance and long-term reliability.
Investing in a high-quality air compressor means investing in performance, productivity, and peace of mind.